As the adverse impact of climate uncertainty (hotter, wetter, stormier, etc.) start having a material impact on businesses, board rooms across industries, will be forced to define and act on ESG (Environmental Social & Governance) commitments.
Product manufacturing and distributing companies of a meaningful size, will have to make parts of ESG a critical component of their business continuity plan, and show they can act on it, within 7 to 10 years.
This article introduces ESG, and lays out some of the capabilities needed off the bat, to effectively implement ESG in supply chains.
First, what is ESG?
Depending on where your company is in its journey, ESG can be:
- Another set of (Reporting) demands, (another blah blah..)
- A framework to design and plan for ESG, or
- A ‘Movement’ towards
Ensuring that companies operate in an:
- Environmentally sustainable,
- socially equitable,
- fair, lawful & balanced way (shareholders, employees, and a healthy planet’s needs)
With a key goal of realizing the environmental & social requirements, while ensuring governance expected, and preventing greenwashing (basically – cheating).
Why is this important?
- to protect the planet’s natural resources, prevent over-consumption without adequate replenishment or mitigation
- to safeguard people directly (and other life forms indirectly), across value chains, and
- to support well-being of communities and societies they operate in (equitably)
- Ensuring that companies continue to supply their products and services, in a timely and cost-effective manner
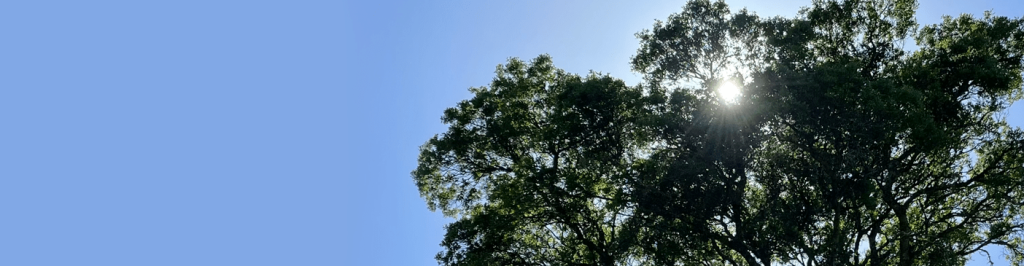
So, what is the issue?
This looks like a win, win, win for all – end customers, product companies, their suppliers (some additional work & costs involved), governments and civic societies.
So, what possibly could be the issue with ESG?
Far too much emphasis is currently being given to Reporting, versus operating in a better manner with respect to real ESG needs.
Necessary but not Adequate – ESG reporting useful, but limiting
ESG data gathering is a critical first step.
Based on Zyom’s direct experience implementing supply chain wide solutions for better understood non-ESG data, across value chain tiers, this is a most demanding exercise, and will be harder given the limited awareness about ESG needs in manufacturing supply chains.
ESG Scoring will be important for implementation success. The challenges – the extremely unique needs of each industry, and a lack of sources of quality data.
ESG Reporting, useful at first glance, is inadequate and insufficient to meet the needs of ESG guided operations. In fact, the reporting emphasis can be limiting, and will dilute focus.
What are the real ESG operating needs?
- How to get ahead of the ESG “regulation curve”?
Especially in terms of designing and defining supply chain partnerships before the regulation hammer falls. This is important for both key and non-key manufacturing, distribution & logistics partners.
Industry context-specific ESG metrics and processes must be agreed to with supply partners at the get go, ensuring, at a minimum:
- Completeness and accuracy of data required to determine ESG risks.
- Agreement on timely ‘shipment’ of supporting ESG data by supply partners
- Alignment on ESG Metrics & Monitoring process
- Process to periodically align on ESG (quarterly, or frequent, e.g., event driven)
2. How to operate ESG ‘aware’ supply chains?
Once the above are in place, operating ESG “aware” supply chains will mean answering these quickly:
- What are ‘out of bound’ ESG events? How to identify such events fast?
- What ‘corrective actions’ need to be taken in advance of such ESG events? Base it on products impacted, supply network’s “segment” impacted, etc.
- How to monitor and ensure the corrective action had its desired impact?
- What are additional costs in case of corrective action?
While some of these appear familiar territory for supply chain operators, some are not. What new capabilities will be needed? Do not go it alone.
Profitability + Sustainability (& ESG needs) – the only way
All of the above will be moot if product supply chains struggle to operate profitably.
For a company to focus in this crucial area of ESG, they must be profitable first, or show a meaningful path to near-term profitability. Only profitable companies will be on solid ground to launch their sustainability efforts from.
Unprofitable companies, or those with a lop-sided dependence on government (or investor’s) money, will most likely, be wiped out, or put another way–
will be toast, making ESG targets even more elusive.
Acknowledgement: Mr. Devesh Sinha, Langan, provided valuable inputs to this article
Disclaimer: No Generative AI was used for composing any of the writeups here (including this one), nor for any data gathering; At this point of time, there is no plan to use Generative AI to generate any content on this site. Readers will be informed in advance if this changes.